With the advent of Industry 4.0, manufacturing companies are adopting predictive maintenance as a new paradigm for managing their production assets.
The new model is based on the automation and digitisation of facilities to enable early detection of disruptions.This new archetype contrasts with the old one, the so-called Run-to-Failure, which only involved manual labour and repair work after the breakage event.
The arrival of new innovative technologies such as the Internet of Things (IoT) and Artificial Intelligence (AI) and increased investment in connected technologies has facilitated predictive maintenance in recent years.
Discover our solutions: Rose Predictive Maintainance
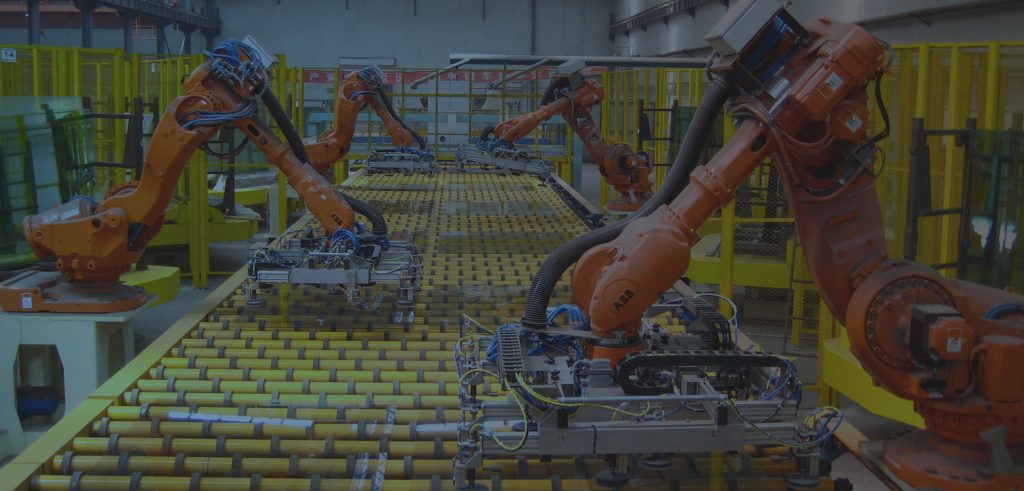
Adopting artificial intelligence and machine learning makes processing large volumes of disaggregated data possible. Thus, a new way of doing maintenance, commonly known as Predictive Maintenance, has emerged.
Predictive analyses extract actionable knowledge and are based on historical data sets. They are used to build mathematical and machine learning models, which can analyse the situation in real-time and predict future breakage events.
Today, companies can apply two types of predictive maintenance to improve their performance
Condition-Based Maintenance (CBM): CBM fits into the anomaly detection field, which has a significant predictive analysis component. This technique involves the real-time monitoring of assets based on certain conditions, either preset or calculated using statistical models.
Predictive Maintenance (PM) is the analysis that predicts abnormal events, thus guiding maintenance actions before the breakage event occurs.
Many studies have shown the growth trends in this market. For example, in 2019, McKinsey & Company published ‘Cracking the code of repair analytics’, an interesting report outlining all the benefits of predictive maintenance. It showed how increasing numbers of companies are adopting Data Science to support decision-making, prioritise maintenance work, carry out efficient planning, reduce costs, and limit disruptions by up to 30%.
In short: predictive maintenance is a valuable tool for managing industrial plants, power grids and substations, renewable energy generation plants and mechanical components. This is because it helps us anticipate risks, plan actions, reduce maintenance costs significantly, and purchase new assets.